
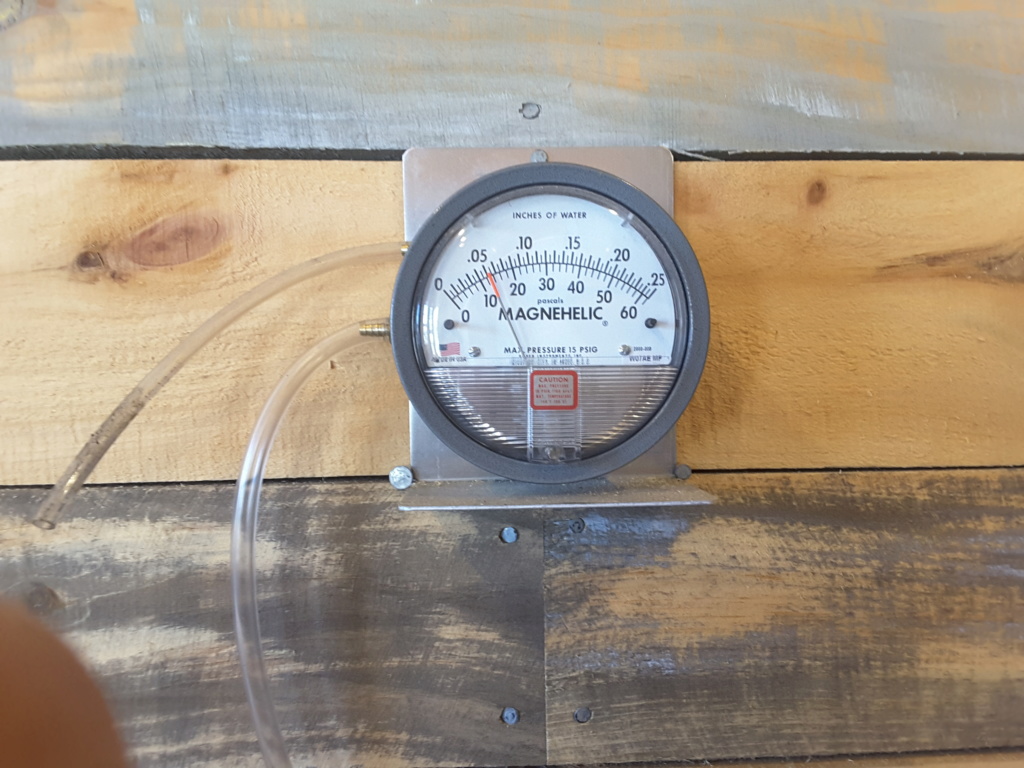
Oxygen injectors used for oxy-fuel or oxygen enriched air supply for combustion.Other components related to process control.Safety system such as shutoff valves, vent valves, etc.Other components associated with process control.Burner air supply control (valves, flowmeters, etc.).Infrared (IR) burners (Radiant, Catalytic, etc.).For electrically heated furnaces, many of these components are not required and the system usually consists of an electrical system version of electricity supply and process-safety-specific components: The heat generation system for gas fired furnaces includes the following components. Furnace functions and componentsĪ typical furnace includes many functions and components for its construction and operation. Each zone temperature is controlled by firing one or more burners operated by a temperature control system. The load may be discharged from the soak zone or it may be cooled in subsequent zones of the furnace. For example, the furnace temperature may be 100☏ at the entry location or zone and it is increased to a much higher value and held constant for one or two zones (soak zones). In furnaces, the temperature is varied in a certain length of the furnace and each length or volume associated with the length is known as a zone. While the load is moving through the furnace, the temperature of the furnace is controlled to a desired value at different locations. In a continuous furnace, the material is placed or loaded directly on a material handling system such as a continuous belt or conveyor and is moved through the furnace to the discharge end (see Figure 1). Here, the ratio of high firing rate to low firing rate, commonly known as the burner turndown is remarkably high. In a batch furnace, the heat requirement may change over a large range and the burner will respond accordingly. Only one set of burners are used, and the burner input is controlled by a temperature control system so the time-temperature requirement is met for the process. In some cases, the load is heated and cooled in the same chamber by using a cooling medium at the end of a heating cycle. At the end of the desired time-temperature cycle, the load is removed from the furnace and transported to another piece of equipment such as a quench or cooling chamber. In a batch furnace, the material is placed in the furnace chamber and is heated by following a certain time-temperature cycle while the load is in the furnace (see Figure 1). The chemical plant and petroleum refinery has their own terminology such as heater, reactor, etc. For example, steel tempering equipment operating at 800☏ is still called tempering furnace in heat treating shop where there are many other high temperature furnaces, while homogenizing equipment in aluminum plant may still be recognized as an oven. Many industries use their own terminology. In many cases a heating equipment operating below 1,000☏ is known as an oven while the equipment operating above 1,000☏ is known as a furnace. It is based on operating temperature considerations, construction based, by a particular industry or even a plant tradition. The terms used for heating equipment such as a furnace and an oven are used interchangeably, particularly in a temperature range of about 800 to 1,400☏. This equipment may use fuel such as natural gas or fuel oil, or electricity as a source of heat. to heat and melt a variety of materials such as steel, aluminum, copper, zinc, lead, magnesium and so on. The metals industry uses heating equipment known as furnaces, ovens, heaters, etc. These facilities receive primary metal sources such as iron ore for steel production, bauxite for aluminum production, metal scrap or an alternate metal source to produce molten metal, which is poured into molds to produce semi-finished shapes such as pigs or ingots, or solidified into slabs, billets or other near net shape products before it is further processed to produce plate, sheet, tubing, bar, rod, wire and other items.

The primary metals industry includes facilities that melt and refine metals from ores and/or scrap metal.
